Far back as I can remember, leaving the front door open was a sin. Coming or going, if you didn’t close the door of our farm house behind you, someone was sure to shout, “Were you born in a barn?” As a kid I heard it so often, I finally decided I was. Later, when I heard about the birth of Jesus, I was amused. How often, do you suppose Joseph or the Holy Mother, when the young messiah left a door open, blurted it out without thinking—I bet they had some good laughs. The other day I heard on National Public Radio (NPR—“Here and Now”) how U.S. households are facing an average heating bill of $1,359 this winter, the highest since at least 1997. And heating bills will rise faster for homes with gas furnaces compared with electric heat pumps. I learned at a young age how frigid a winter floor can become near an open door or in front of our old brick fireplace. I remember falling asleep in the draft of my leaky bedroom window.
Leaks do matter. That’s why air-tightness is so important in Passive House building. I’m such an intermittent blogger I must begin again by reminding you of PH building standards for our house:
1. Orientation to the Sun
2. Super Insulation
3. Air-Tight Construction
4. High Performance Windows
5. 24/7 Energy Recovery Ventilation (ERV)
6. Thermal Bridging-Free
In order to benefit from a south orientation, winter heat gain from high performance windows, thermal bridge-free construction, super insulation and 24/7 heat recovery ventilation we need a tight house. In winter, air-tight construction minimizes cold air infiltration from the outside and warm air leakage from the inside. In summer, a sealed home keeps hot air out and cool air in. Having said that, I’m amazed at how many times, in conversations about air tightness, a carpenter or contractor (pros who should know better) will say, “But houses need to breathe!” This is totally true, but in air-tight PH building, we choose to control the breathing with a ventilation system instead of random leakage. In winter, our Zehnder ERV exchanges the heat from the warm outgoing air to the fresh, cold incoming air as the two streams pass. This sustains the indoor heat we would otherwise lose through the inferior construction of an unsealed house.
Infiltration from outside and leakage from inside a building envelope is measured in Air Changes Per Hour (ACH). 1 air change per hour means all air inside the house is completely replaced with outside air once each hour. 2 ACH means the house leaks enough to replace all inside air with outside air twice each hour and so on. 6 ACH means leakage allows inside air to be completely replaced with outside air 6 times each hour! The leakage is measured by placing a big blower in the front door, then pressurizing and de-pressurizing the house to 50 pascals of pressure.
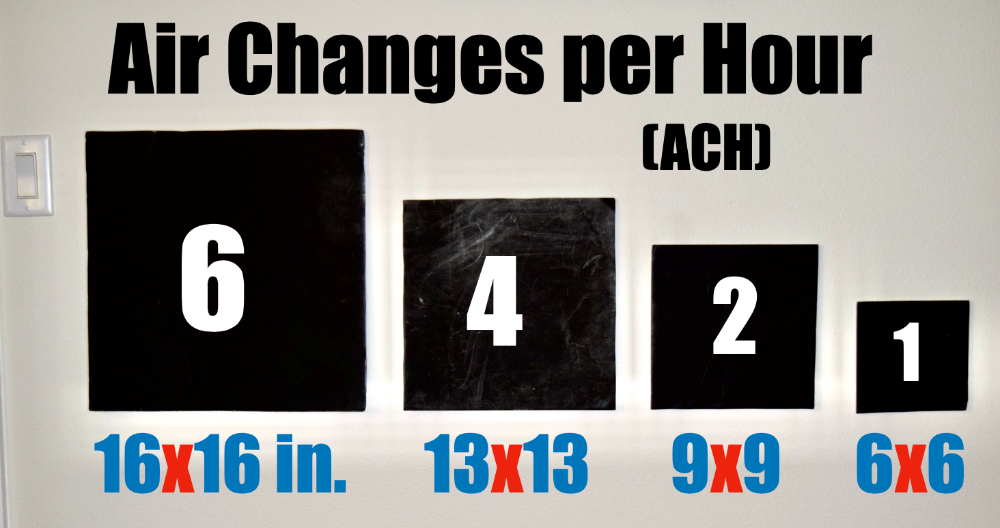
Our friends at AeroBarrier NW, here in Bend, have created these black squares to help us visualize Air Changes Per Hour. See that if we have enough leaks in our building envelope to add up to 6 Air Changes Per Hour, it’s like living in a house with a permanently open window 16 inches square. 4 ACH is like living with an open window 13 inches square, 2 ACH, living with a 9 inch window open and 1 ACH a 6×6 inch opening. Now these calculations were measured on a 2500 sq. foot home with 9 foot ceilings and 6×6 inch open window in our 1,000 sq. foot home will have a greater impact than the same in a home 2-1/2 times the size. But you get the point!
Well-built conventional homes will test between 5 and 6 ACH. To be a certified Passive House we had to test right around 1 ACH! The PH standards have changed a bit since we built our first 1,000 ft2 Passive House in McMinnville in 2016. At that time, our home had to test at .6 ACH or less. We actually achieved a leakage score of .51 ACH! The standards are more flexible now, taking into consideration all the different variables of construction so we had to test somewhere close to 1 Air Change Per Hour this time. And here is where the story gets interesting, at least if you’re an uptight house nerd!
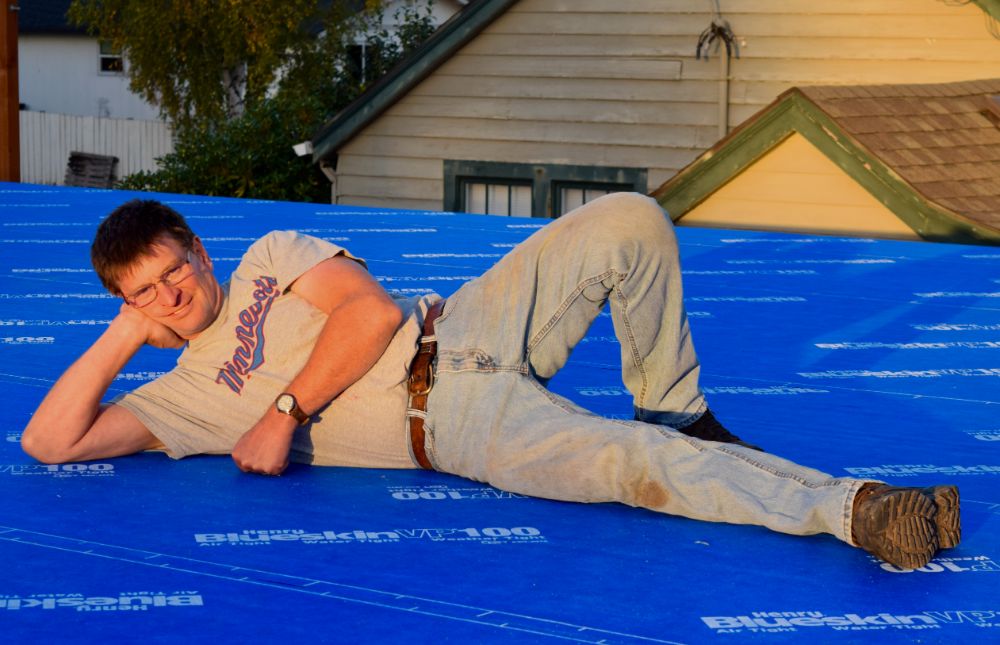
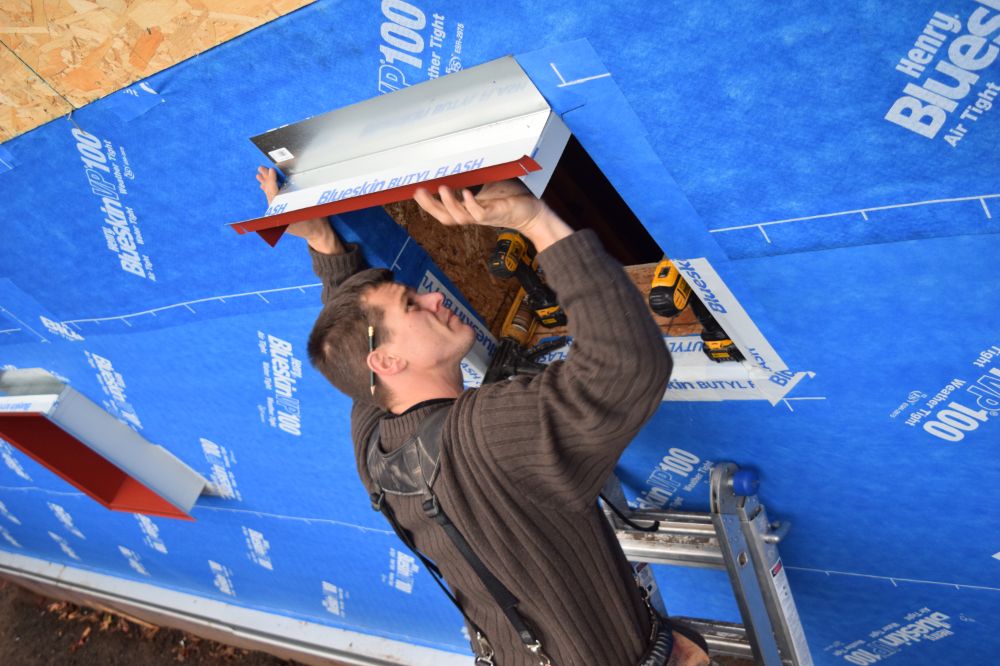
The envelope of our McMinnville Passive House was sealed with Blueskin® VP100 Self-Adhered Membrane, Henry’s Blueskin for short (https://henry.com/). This is a blue, sticky-backed, material that, when punctured by a screw or nail, self-seals. Beside its obvious sealing properties, when applied to the outside of the sheeting on walls and ceiling, it provides a stunning cobalt photo op for the local Blueskin Diva!!! Two carpenters were trained to crease and fold the skin around doors and windows like a Christmas gift wrapped at the store. We passed our leakage test the first time with flying colors—.51 ACH. You might see why Henry’s is required on all new construction in California now.
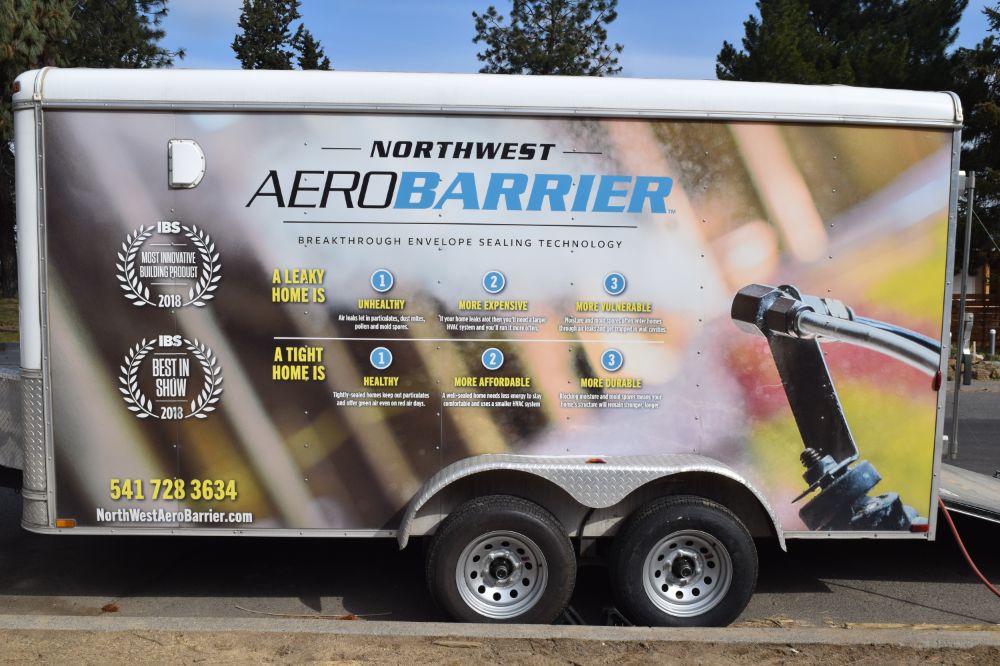
For our Bend Passive House, we built the same design, but our builders didn’t have any experience with BlueSkin. It turns out, though, in the time between 2016 when our Mac house was completed and 2022 when our Bend house was built, AeroBarrier (https://northwestaerobarrier.com/) became available. Though invented in 1993, AeroBarrier really broke onto the construction scene in the Pacific Northwest just 3-4 years ago and an office of AeroBarrier NW, ready to seal houses with Aeroseal (https://aeroseal.com/), opened in Bend. Our research showed this was a real game changer in the field of air-tightness, so we decided to seal this house a totally different way than before.
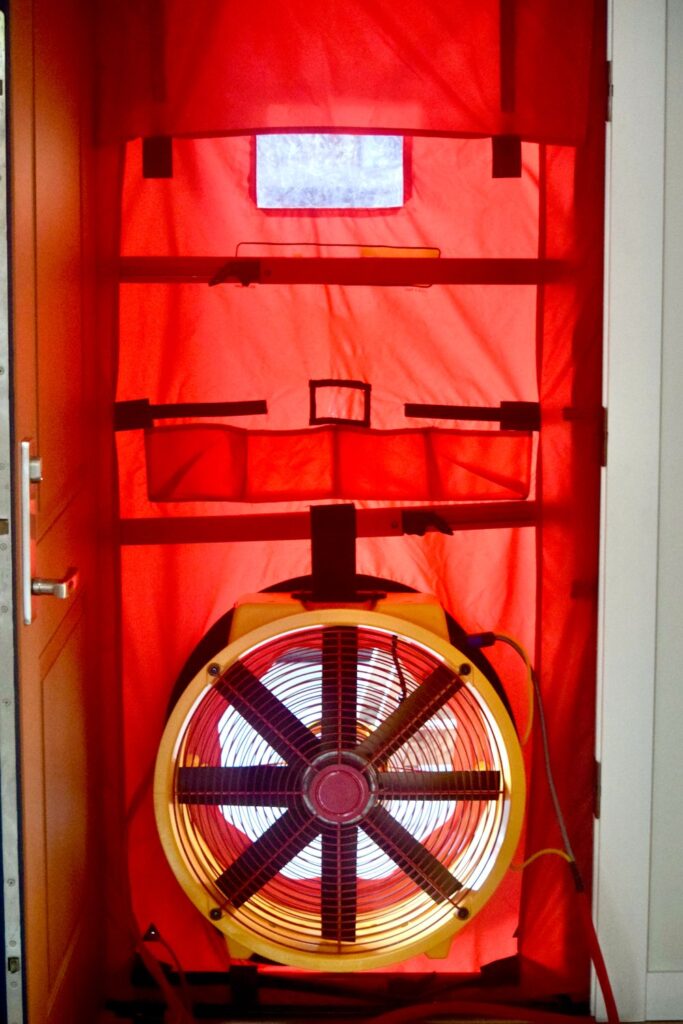
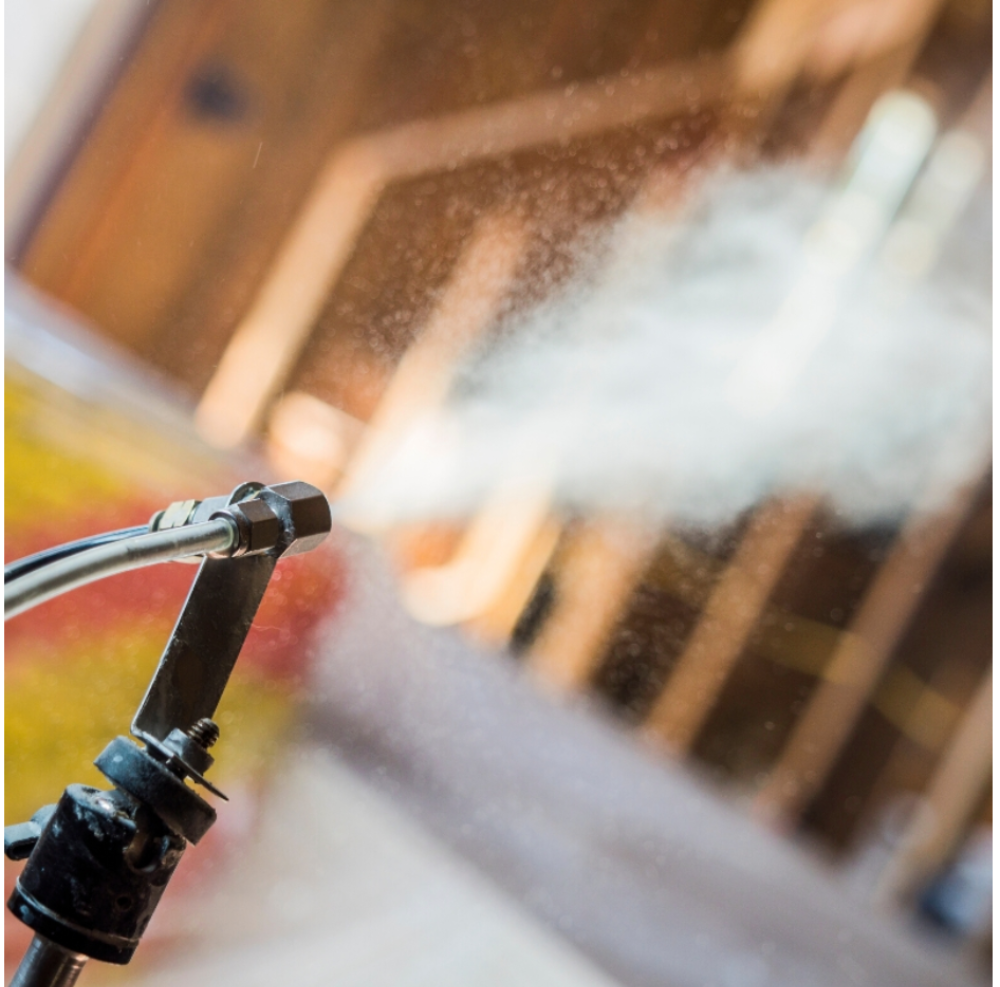
AeroBarrier’s website says Aeroseal is a “stable, non-toxic, non-flammable emulsion of water and vinyl acetate polymer aerosolized into 4-10 micron-sized particles, distributed under pressure inside the building envelope.” This is so deeply nerdy, but I like to think of it as a liquid caulk in aerosol form or, if you prefer, boogers on steroids. When the building envelope is completed, houses are pressurized with a blower door while spray nozzles fill the interior with the aerosol spray. With the pressure turned up high, the aerosol droplets start accumulating in every hole, crack, nook and cranny, until all the leaks in the envelope are sealed. In this application, holes as large as 1/2 inch can be completely plugged to reach extremely low ACH readings.
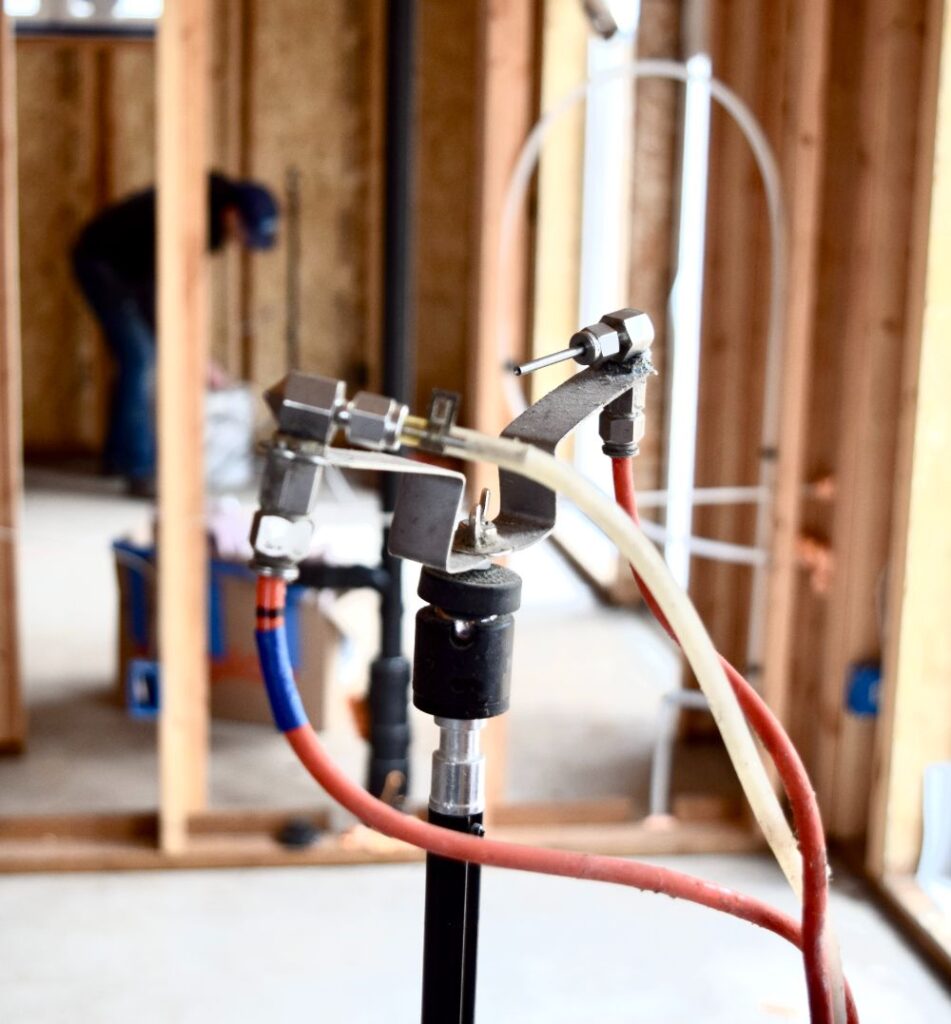
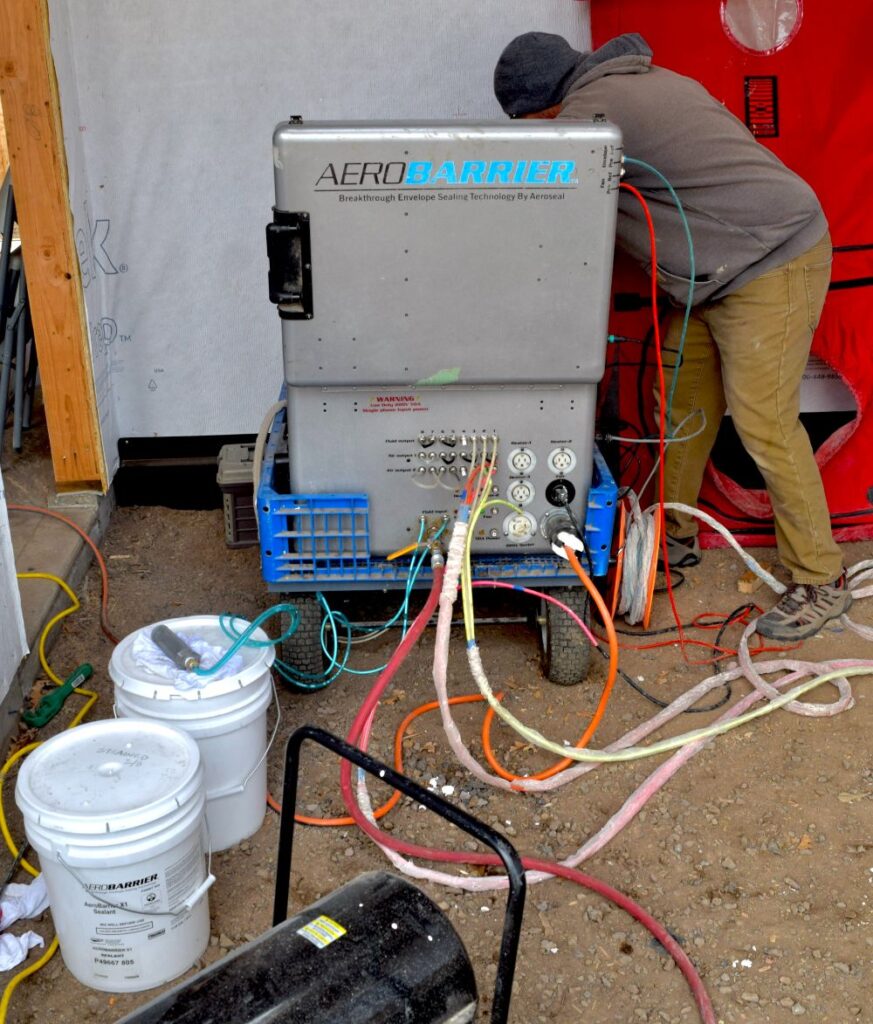
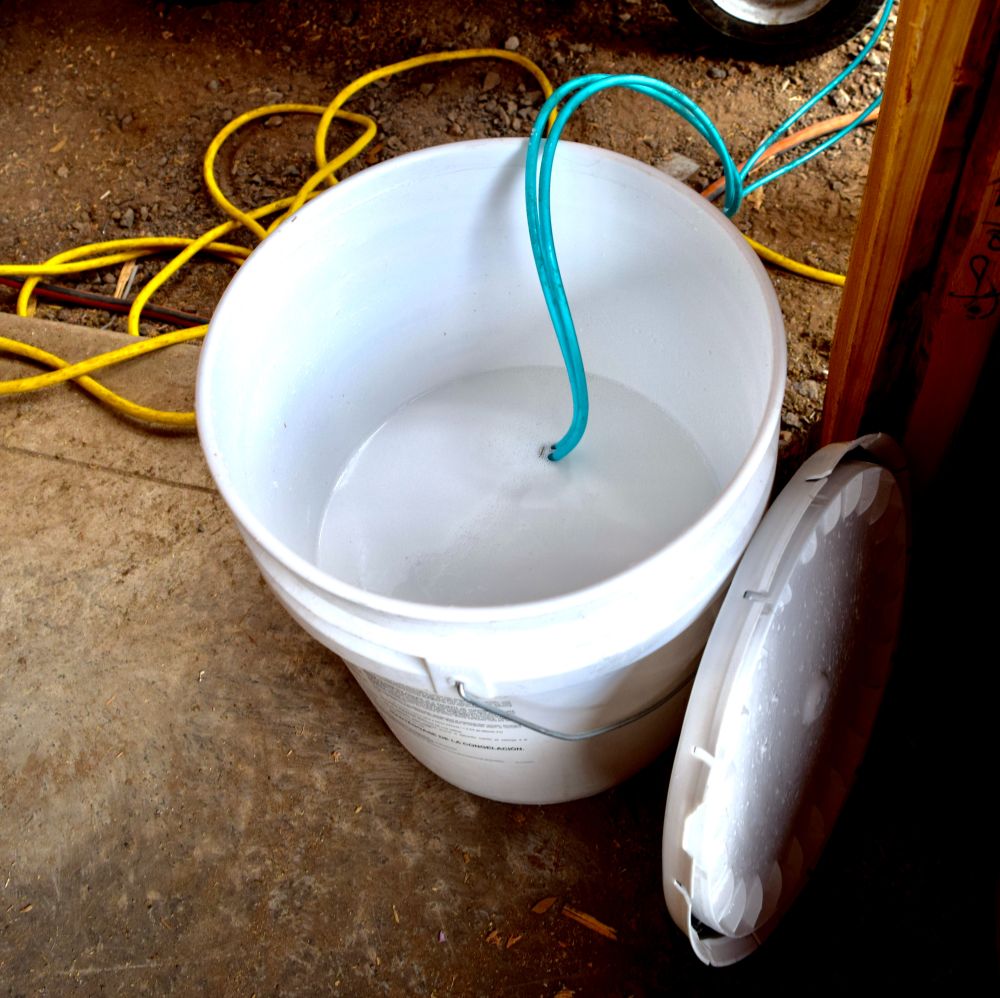
When our building envelope was complete, the day for AeroBarrier arrived. The truck pulled up in front of our house and the team went to work, placing one spray nozzle in the living room and another in the front bedroom. They set up their pumping machine, inserted the blower door and the elixir began to flow through tubing from five-gallon-buckets to the nozzles on the inside.
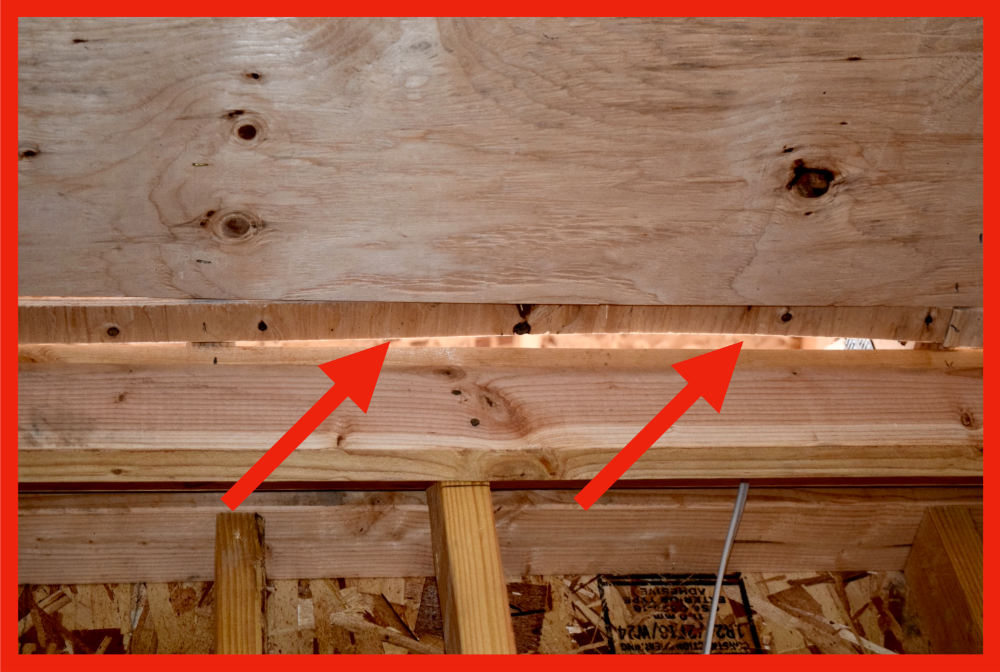
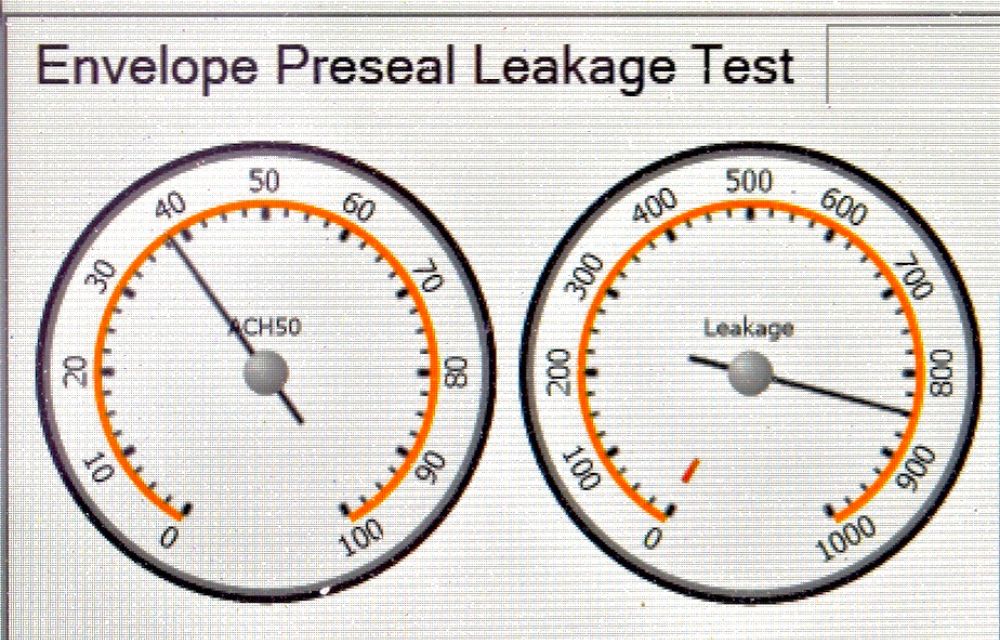
Now, I wish I could tell you that the whole treatment process went seamlessly (I guess that’s a pun)…that we were done in a couple hours. That’s how it’s s’posed to go. But we had a situation. Apparently the subcontractor in charge of completing the envelope got super excited when he heard of this new AeroBarrier thing. He went on line and read all he could about it, which was great. Enthusiastic builders are a good thing. But he must’ve come to the conclusion that this new fangled sealer would work like magic so one wouldn’t necessarily have to stress over building the shell of the house super tight to begin with, because the magic would cover all mistakes. So what does it matter if the sheet of plywood doesn’t quite reach the ceiling joist and we leave a quarter inch crack 4 feet long over the bathroom? There were so many cracks, when they cranked up the blower to get a baseline reading before the AeroBarrier was applied, the technicians couldn’t believe their eyes. The meter read 38 Air Changes Per Hour! Yes 38! Our house was leaking like a virtual sieve!!!! More hand caulking was done in the attic and we got the reading down to 14 ACH before starting the aeroseal process. It still took 7-8 hours instead of 2-3 and we used a ton more of the gunk than planned. But when complete, we got the leakage down to .2 ACH.
And I wish I could tell you that was the end of the story, but no. The heat recovery ventilating unit, which was to be mounted in the attic didn’t arrive until after the sealing was done. Meaning the installers had to break the seal to position the unit correctly. When the day came to do the final blower door test, we couldn’t meet the 1 ACH standard. We did more hand caulking but still too many leaks! We finally had to vacuum 27 inches of insulation out of the attic so we could find the leaks and seal them. That was a pain in the butt, which is why, when we finally passed the leakage test at 1.o9 ACH we had to take a celebration pic of Geoff our contractor, Matt the Earth Advantage blower door guy and myself. WE FINALLY MADE IT! I took these photos of how a couple of our cracks looked after the treatment.
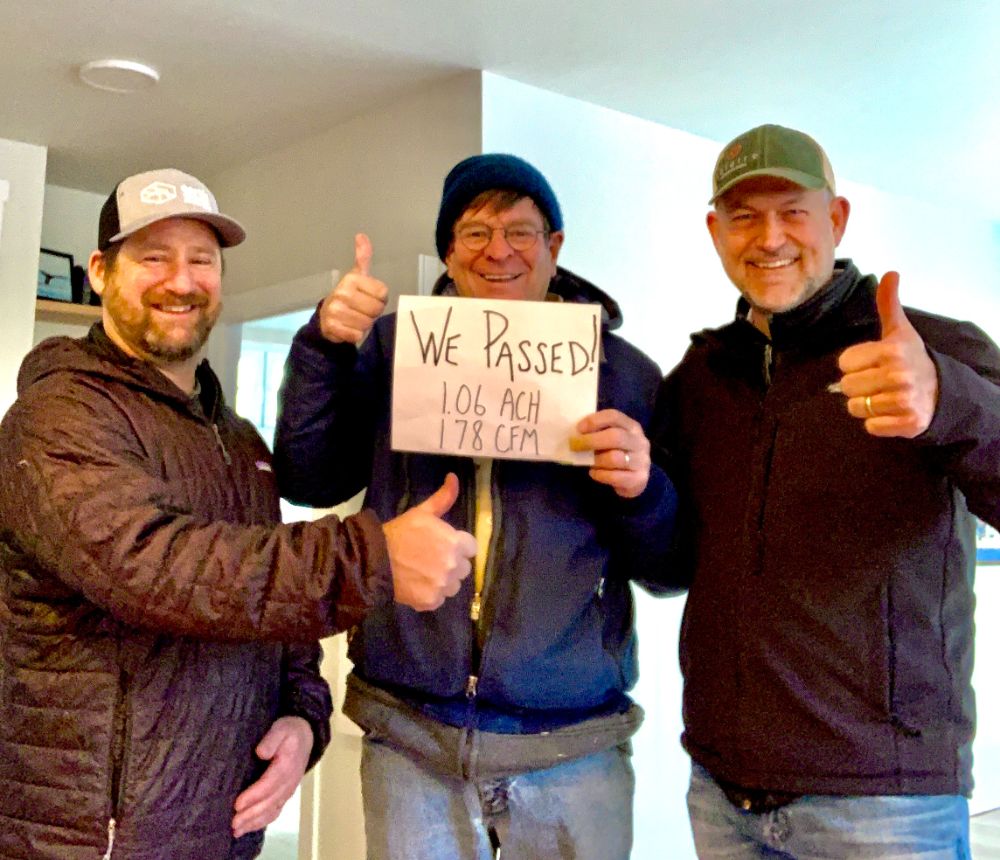
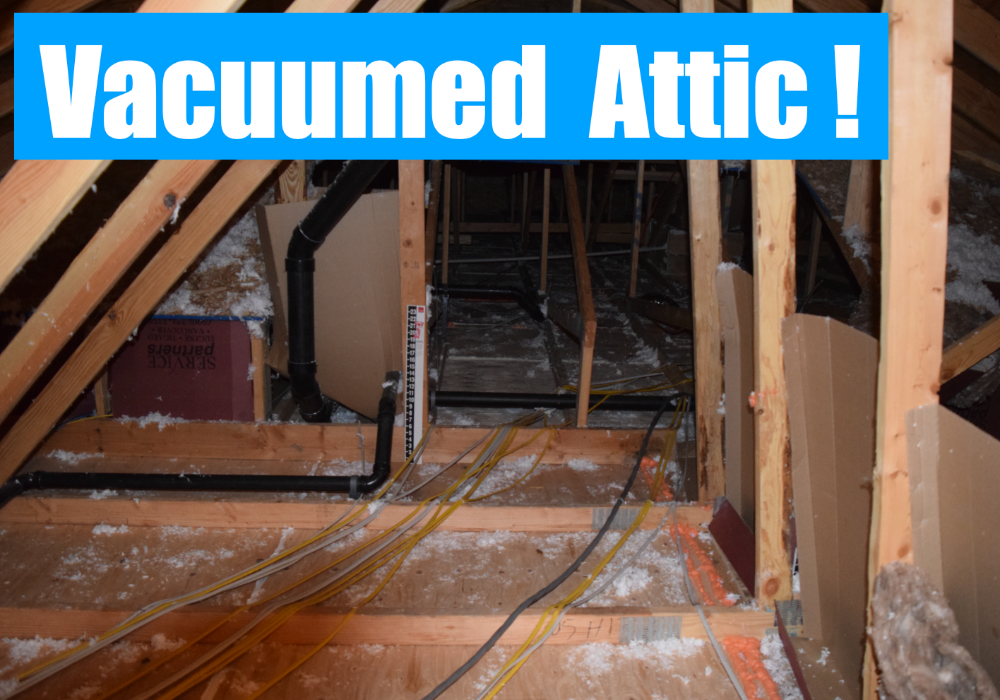
Now I have to be clear. AeroBarrier NW was responsible for none of the adventures we had in the process of sealing our building envelope to meet the Passive House standard! So far, at least 150,000 U.S. homes have been sealed with Aeroseal. It is truly a game changer. Believe it or not, the AeroBarrier treatment can even be done on existing homes to reach the same standard for air-tightness as our our newly constructed building.
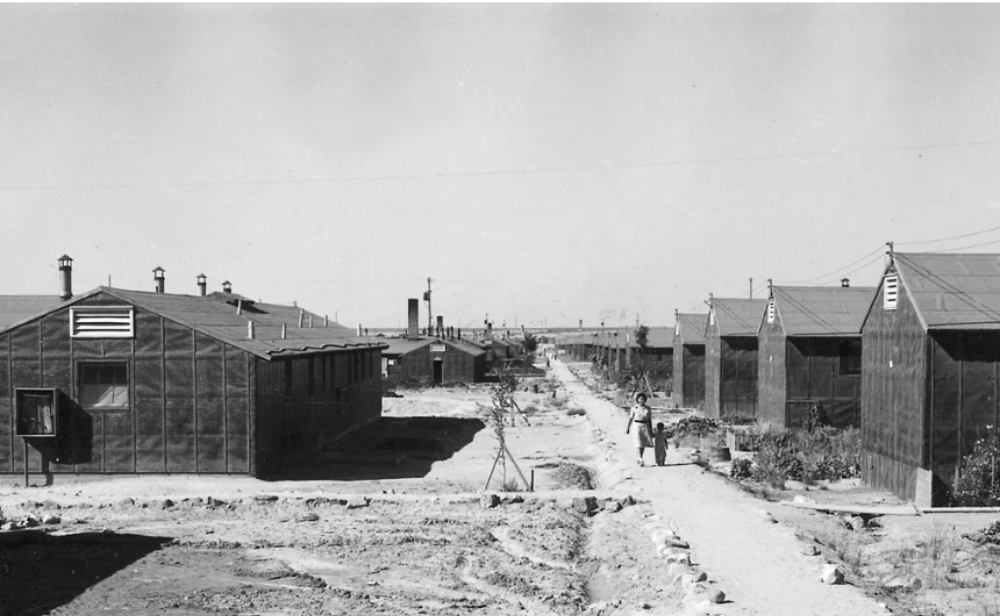
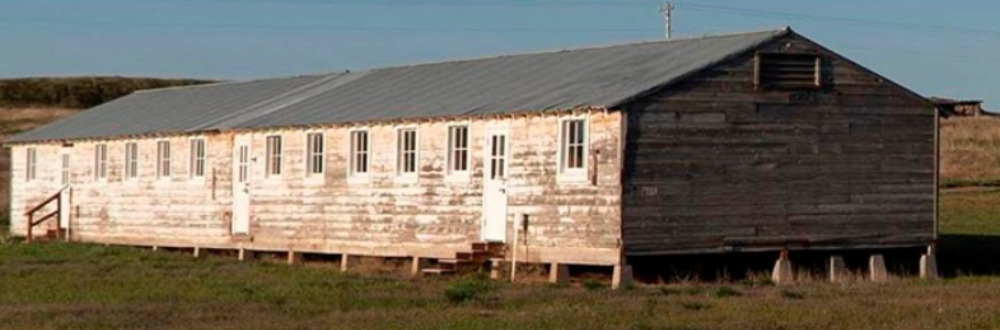
As I prepared for this blog, I remembered touring a farmworker housing encampment near Twin Falls, Idaho for a conference on farmworker justice in the 90s. Our hosts told us these buildings, currently housing farmworker families, had been moved there from the Concentration (internment) Camp at nearby Minidoka where Japanese American citizens and their families were incarcerated during WWII. As we walked among these buildings, which reminded me of the chicken barns of my youth, we could see families inside through wide cracks in the old ship lap walls. In a stroke of American racist ingenuity, we efficiently re-purposed drafty buildings from one site of violence to another. Sadly, our legacy continues to be that tribal folks, other people of color and those on the margins get the leaky house and or the barn-like housing they can’t own but nobody else wants. Likely, if they have housing at all, they and their descendants will be born (in a barn) and die there. I said at the outset that, as a kid, leaving a door open was a sin. If sin is separation from the Divine and the humanity we were born to be, forcing human beings to live in buildings where the ACH is equivalent to permanently open doors and windows, must put us all in some kind of cultural purgatory! In a world like ours, a story of a child born in a barn under a star, is at least hope that there’s someone who understands what that’s like. More of us need to understand.
If I have hopelessly veered from my lane, I apologize. But leaks do matter. And just the simple story of our personal adventures with aerosol home sealer will likely fall like a thud on the deaf ears of a few privileged whites and never register as a public good. But I said AeroBarrier is a game changer. The application is simple. If it can even be applied to existing homes, apartments, affordable housing and beyond…what if it were set in building code? Actually maybe I should tell you that an ACH reading of 4 or better is already required in Oregon Building Code for new buildings. What if this were actually enforced? What if it was a real standard, part of every dwelling, no matter what the zip code? The bill I and many volunteers advocated in the 2022 Oregon Legislative Assembly would have allowed Oregon municipalities to set codes (called “Reach Codes”) more strict than Oregon Code. It would have allowed towns and cities to go beyond into a vision of the future of what we all must be.
The builder and realtor lobbies killed it last year, but a commission was established to suggest code changes at the state level and report back to the 2023 Legislature for action. If you are an Oregonian, call, email, text your representative and senator to ask about this. Ask them to support building code changes for all Oregon human beings. (https://www.oregonlegislature.gov/)
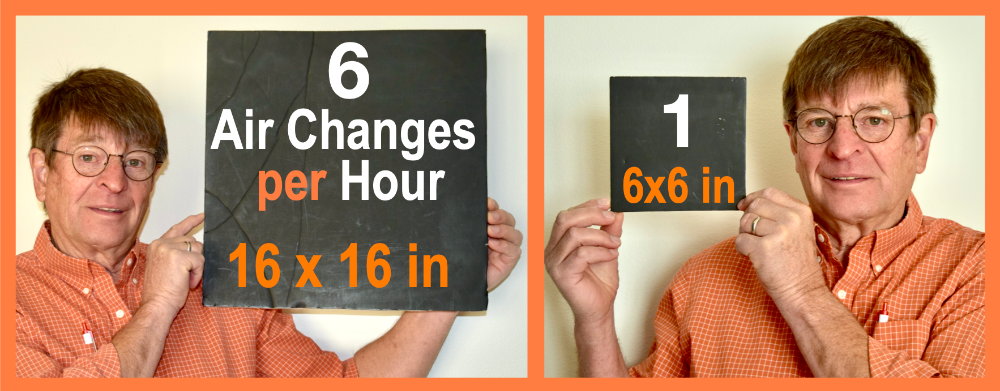
In the meantime, if anyone asks “Were you born in a barn?” Before you wax eloquent about Air Changes Per Hour, Aeroseals, aerosols or the inequities of where we force people to live…maybe just close the door! Then wax!
John. Nice application of experience based repentance and the cost of housing justice. I expected an air test at our final inspection. It turns out Spokane County which is in an extreme temperature zone of highs and lows overlooks this as part of enforced building code. We are in a sea of red here. Miss you and all of our Oregon Peeps. Elwyn
Great information John. Thank you Would it be all right if I shared this with some friends?
Well, I surely did just learn a lot, reading this! As a carpenter’s daughter, living in several houses while they were being remodeled, I could understand what you were talking about EASILY! Still, I have this one reservation:
My elderly house is only slightly older than I am, with most of its original double-hung windows (which I love; I hate the bronzed-aluminum double-paned tinted sliding windows that replaced the old windows on the front side of the house.) In winter I stuff strips of old plastic shopping bags between the two parts of the window, and it helps enormously. But I’m afraid if I replaced these drafty devils with supersealers, I wouldn’t hear the birds outside. Can you hear the birds?
John,
I can’t get anyone to insulate the walls in my 1949, prefabbed in Corvallis and moved to Springfield, house. The plaster board is ¼” and was put in with nails. My recent excellent exterior paint job removed all traces of the unused circles left by the insulating company when they refused this work. The sheetrock cracked and nails stick out when they did the first 5 foot area.
Do you think the AeroBarrier process would work inside my walls?
Where do you access inside the walls?
My attic has 65 years of 4 layers of insulation removed and then the house was sealed off from the attic space. Then the attic was well insulated. It now has to be raining very hard for me to hear it. :~)
Ideas?
John,
I love reading these nerdy posts. You are an inspiration to do better.